High Performance Machine Taps
- Long Tool Life
- Reduced Cost
- Excellent Thread Quality
- Superior Process Security
Machine Taps removes material from a pre-drilled or punched hole. The result of this cutting action produces threads within the drilled hole.
These threads are used in conjunction with screws or bolts to hold two pieces of material together. The cutting edges at the front of a tap remove material from the workpiece. The chips are stored in the flutes, or pushed forward in front of the tap, or are drawn up along the flutes, removing the chips and cutting fluids from the hole.
- Taps typically have several flutes constructed in its design. They are the grooves or valleys cut into the body of the tap. Higher numbers of flutes increase the strength of the tap and reduce space or chip flow.
- Thread size is the number of Threads Per Inch (TPI) which is measured along the length of the tap. Metric sizes are referred to as thread pitch.
- Chamfers are the length of the tapering threads at the front of the tap. Both the chamfered portion of the tap and the first full thread beyond the chamfer produce the finished thread of the part.2
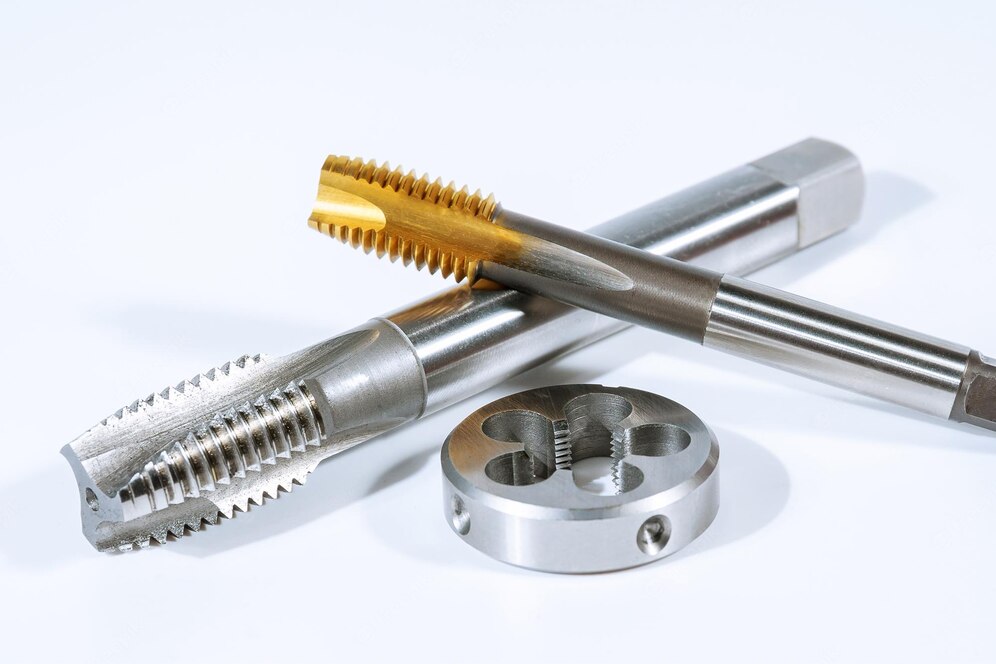
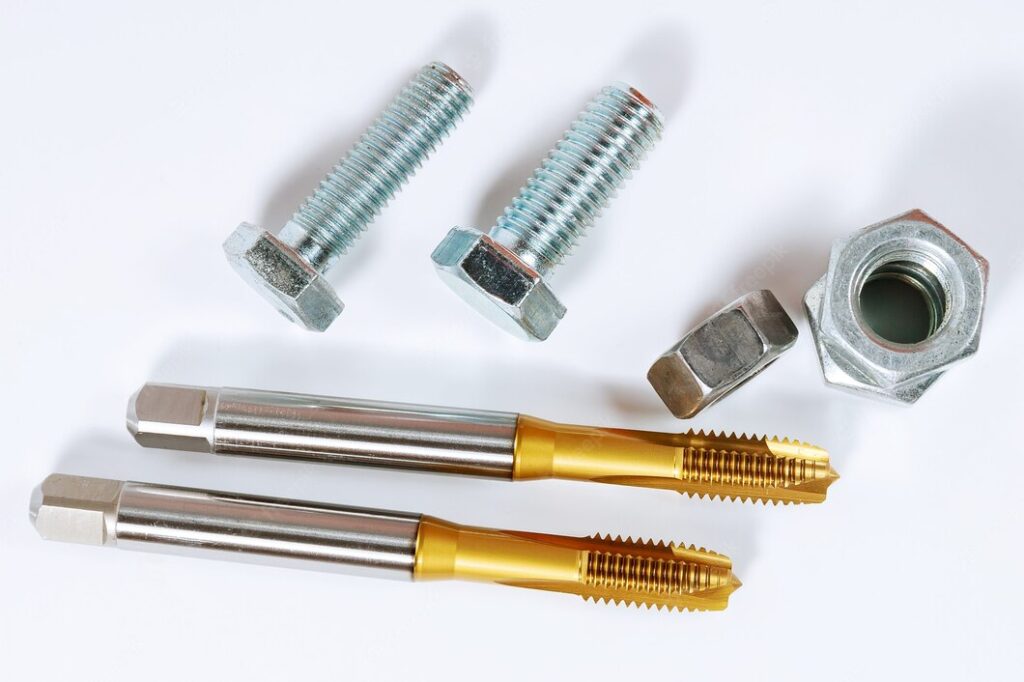
Type of Machine Taps
Thread forming taps do not cut threads; rather, they form threads by removing material. They generate threads without producing chips. They are used on mild steels, carbon steels and low to medium alloys.
Straight flute taps are used to create threads in through holes or blind. They can be used by hand or in general purpose machine operations.
Spiral flute are designed with flute geometry that draws the chips away from the hole. It helps to resolve the chip disposal issue. These taps are used for threading blind holes in aluminum, brass and softer steels.
Cutting Material
- Sturctural Steel
- High Carbon Steel
- Medium Carbon Steel
- Low Carbon Steel
- Alloy Steel
- Hardended Steel
- Mold Steel
- Pre Hardended Steel
- Stainless Steel
- Cast Iron
- Ductile Cast Iron
- Copper Alloy
- Titanium Alloy
- Aluminium Alloy
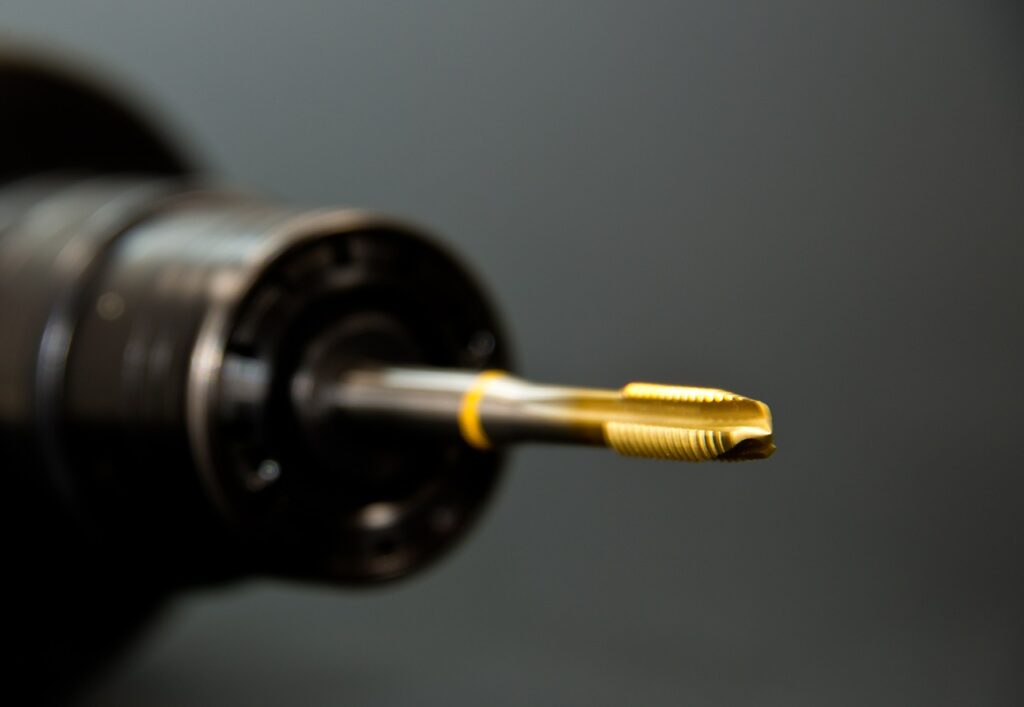
Benefits
Long tool life reduces costs
Solid taps are made of high-speed steel with cobalt, high-speed powder steel, carbide or tungsten for superior wear resistance and tool life resulting in fewer machine stoppages and reduced cost-per-hole.
Excellent quality of Threads
To ensure low friction at high speeds for precision thread forming with minimal surface roughness
Superior process security
Optimised lobe profiles allow for reliable, predictable tool life at high cutting speeds for both through- and blind-holes.
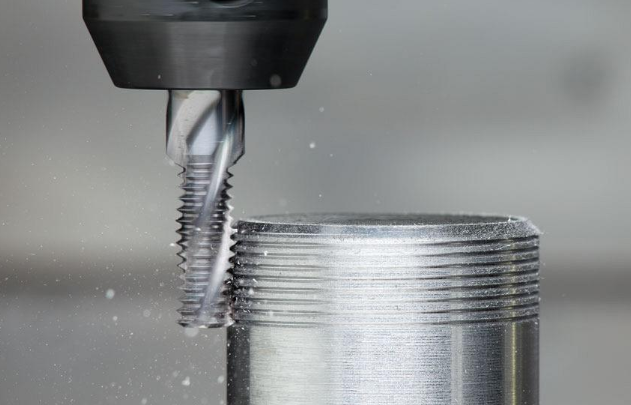
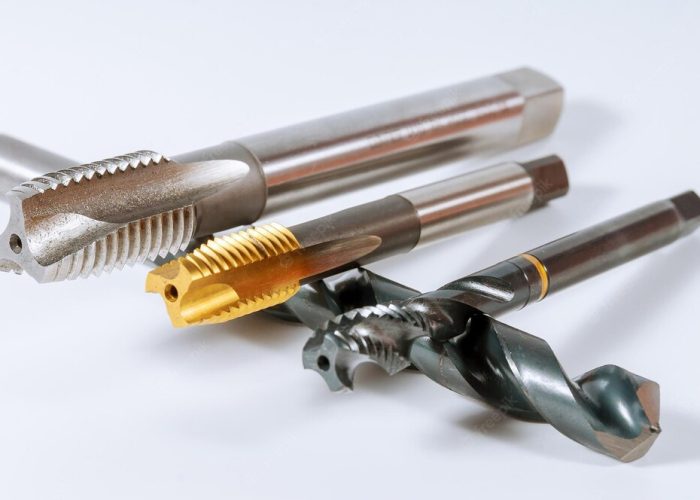