Wide Rage of Endmills
We have high precision End mills that are specifically designed for optimum performance in a wide range of materials and machining applications
For Milling, Contouring, Slotting, Counterboring, Reaming Profiling and Drilling Applications
Cutting Material
- Sturctural Steel
- Carbon Steel
- Alloy Steel
- Heat Treated Steel
- Hardended Steel
- Pre Hardended Steel
- Stainless Steel
- Cast Iron
- Titanium Alloy
- Copper Alloy
- Alluminium Alloy
- Graphite
- Heat Resistant Alloy
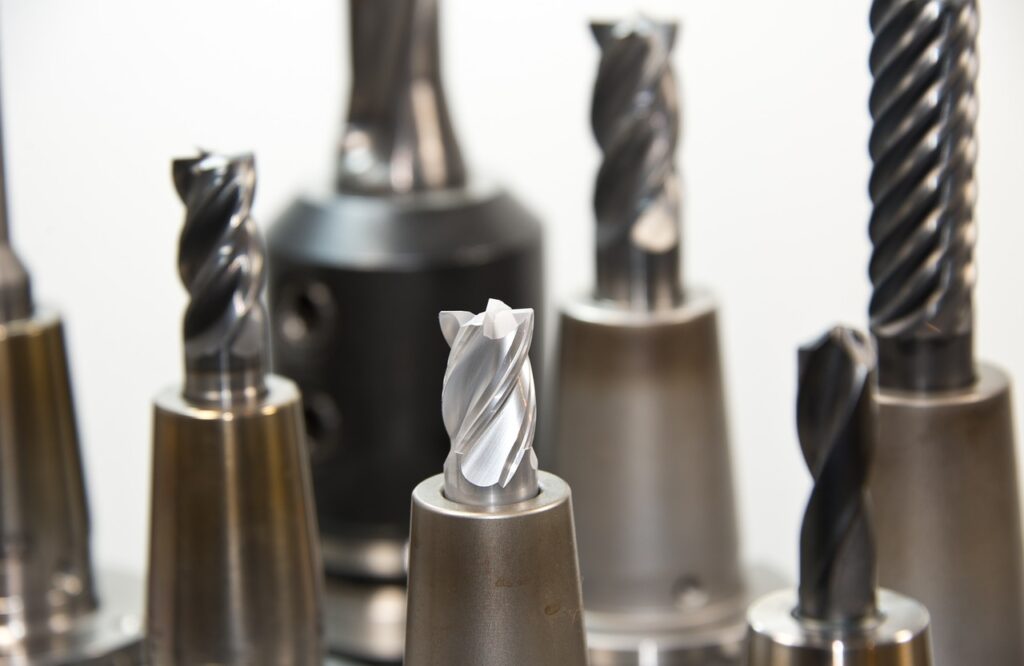
Endmill Material Type
Provides good wear resistance and costs less than carbide or cobalt endmills. HSS endmills are used for general-purpose milling of both nonferrous or ferrous materials.
Provides superior wear resistance, greater hot hardness and toughness than high speed steel (HSS Endmills). There is very little chipping or microchipping under harsh cutting conditions, allowing the tool to run 10% faster than HSS, resulting in excellent metal removal rates and good finishes. It is a cost-effective material ideal for machining cast iron, steel and titanium alloys.
Is tougher and more cost effective than solid carbide. It is tougher and less prone to breakage. PM performs well in materials < 30RC and is used in high-shock and high-stock applications such as roughing.
Provides better rigidity than high-speed steel (HSS). It is extremely heat resistant and used for high speed applications on cast iron, nonferrous materials, plastics and other tough-to-machine materials. Carbide end mills provide better rigidity and can be run 2-3X faster than HSS. However, heavy feed rates are more suitable for HSS and cobalt tools.
Flute Type Available
Flutes feature depressions or grooves that are cut into the body of the tool. End mills with less flutes on the cutting edge will have more chip space, while end mills with more flutes will be able to be used on harder cutting materials. Higher number of flutes increases the strength of the tool and reduces space or chip flow.
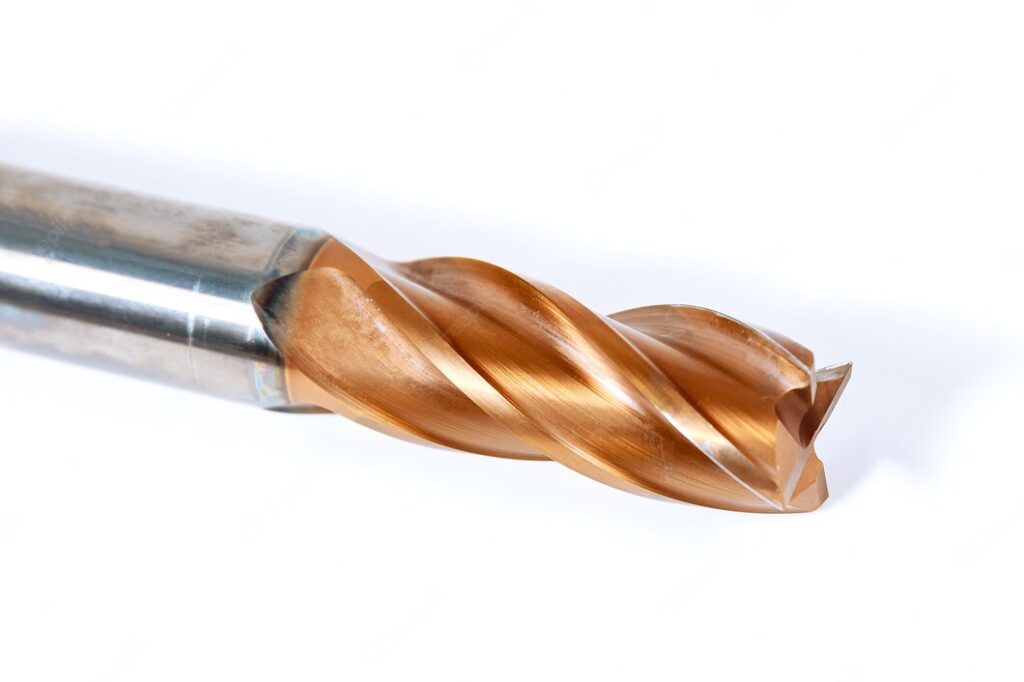
Two Flute designs have the most amount of flute space. It allows more chip carrying capacity and is used primarily in slotting and pocketing nonferrous materials.
Three Flute designs have the same flute space as two flutes, but also have a larger cross-section for greater strength. They are used for pocketing and slotting ferrous and nonferrous materials.
Four/Multiple Flute designs allow for faster feed rates, but due to the reduced flute space, chip removal may be a problem. They produce a much finer finish than two and three flute tools. Ideal for peripheral and finish milling.
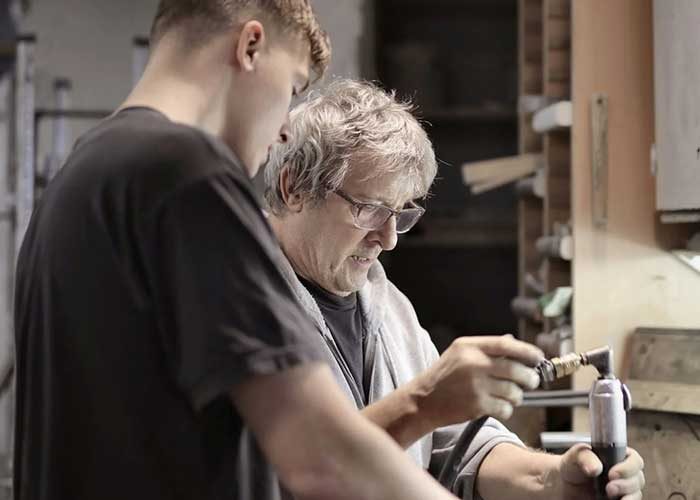