High Performance Drills
Designed to carry out critical operations late in the production cycle when the component value is already high
In today′s competitive environment, getting the most out of your tooling is vital. electing the right tool material is a big step toward maximizing productivity and reducing cost per hole. Investing in drilling is an easy way to improve your bottom line
Drill Material
- Combines good tool performance and productivity with minimum cost
- Works well in non-ferrous materials like aluminum, brass, bronze and copper, as well as free cutting and carbon steels.
- With the right point angle and helix, it is the most cost-effective for machining cast iron, heat-treated steels and titanium alloys
- Able to handle less than ideal set-ups
- Heavy feed rates are more suitable for HSS and Cobalt tools
- Designed For high-performance applications
- It can run faster and withstand higher temperatures, while providing good wear resistance
- Provides better rigidity than HSS, yielding a higher degree of dimensional accuracy, often eliminating the need to ream
- It is brittle, and tends to chip when conditions are not ideal
- Solid Carbide Drills is used in abrasive and tough-to-machine materials: cast iron, non-ferrous alloys, glass, plastics and composites
Work Material
- Sturctural Steel
- Carbon Steel
- Alloy Steel
- Heat Treated Steel
- Mold Steel
- Pre Hardended Steel
- Stainless Steel
- Cast Iron
- Ductile Cast Iron
- Copper Alloy
- Alluminium Alloy
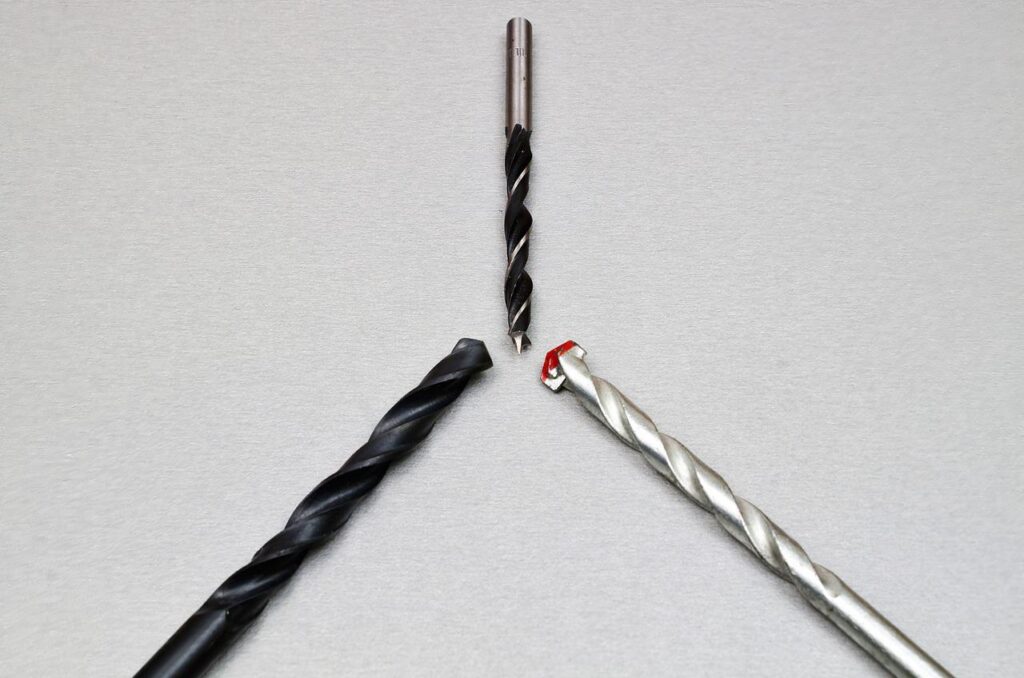
Drill Style, Grade and Length
There are wide variety of choices in the market, finding the right drill can be difficult. Using the diameter and depth of the hole, amount of holes you need to make, work material and the type of job we can help you in selecting the right Drills for the Job
Styles:
Straight Shank Drills are the most common style in the world. Shank size always matches the cutting diameter.
- Twist Drills are the most widely used style in the world. For use in the widest application in ferrous and non-ferrous materials
- Parabolic Drills are for deep-hole drilling, reducing the need to peck
- Slow Spiral Drills are used for long chipping materials, such as aluminum and copper
- Fast Spiral Drills are used for small chipping materials like stainless steel
- Half-Round Drills are used for deep-hole drilling of very soft materials, like brass and rubber
- Straight Flute Drills are designed to drill the hardest steels
- Core Drills are used to enlarge existing holes
Taper Shank Drills are long length drills that are fitted with a special shank called a Morse Taper. These drills are made specifically for spindles that can hold Morse Taper shank drills.
- Taper Shank Drills come in many styles: Stub Length, Extra Long, Core Drills, Hi-Helix, Slow-Helix and Coolant-Fed
Grades:
- General Purpose are perfect choice for maintenance, repair or short production runs in soft ferrous and non-ferrous materials.
- Heavy-Duty drills typically combine a split point to prevent walking, and stronger flutes for better rigidity. They are an excellent choice when drilling harder materials
- High Performance drills are typically designed for application specific operations where productivity and cost per hole is a concern
Lengths:
- Screw Machine – Stub length
- Jobber – Standard length
- Taper – Long length
- Extra Length
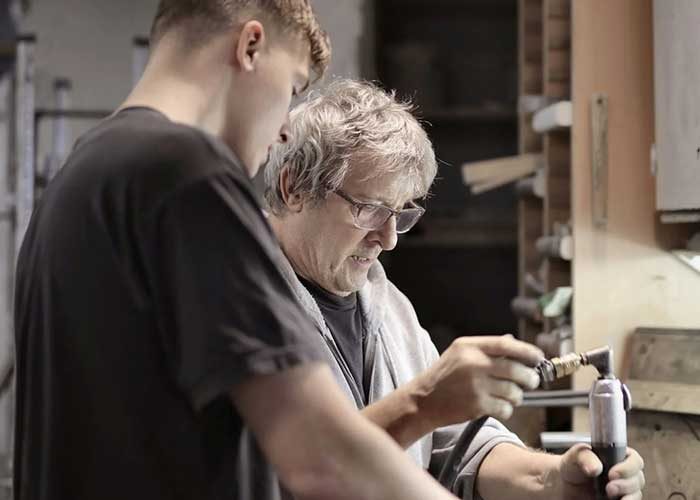